Life-Cycle Assessment Considerations for Batteries and Battery Materials
This is a summary (plus, a few of my own thoughts) of the review article “Life-Cycle Assessment Considerations for Batteries and Battery Materials” (2021) by J. Porzio and C. D. Scown.
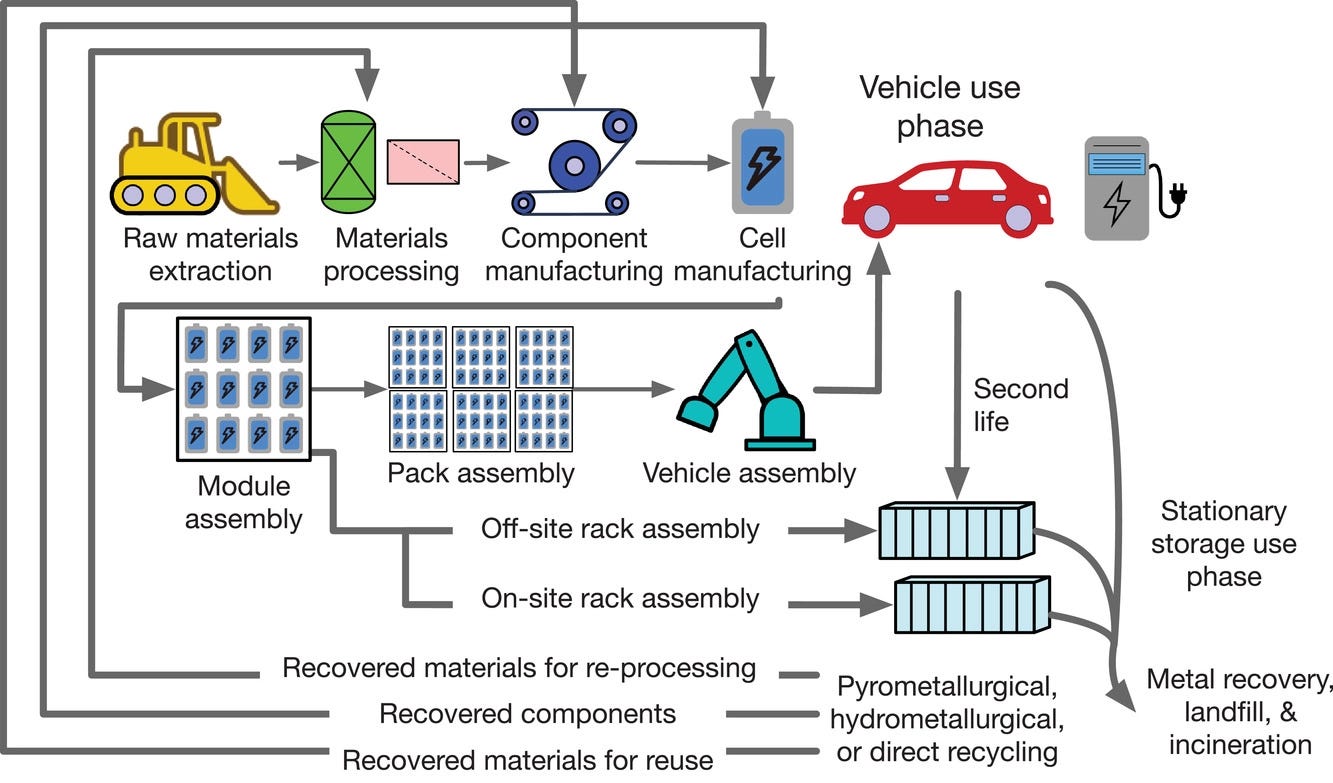
Types of battery life-cycle assessment
There are two main types of battery life-cycle assessment (LCA): "cradle-to-gate" and "cradle-to-grave".
Cradle-to-gate (factory gate is assumed here). The example metric is CO2e/kWh of battery capacity produced. In a truly use-agnostic LCA, the system boundary may need to be set at the module assembly stage, since the assembly of the pack or rack (including such components as thermal management and electrical control) will differ substantially depending on how the battery will be used.
"Cradle-to-gate and use" is a variation that incorporates battery manufacturing and lifetime of usage, but not end-of-life recycling.
Cradle-to-grave LCAs consider how batteries will be used and treated at their end of life including collection, recycling and/or disposal.
The term cradle-to-cradle has been used to refer to systems that include recycling, but is generally meant to suggest a zero-waste process and thus is not commonly used to refer to battery life cycles, even if they include recycling.
Midpoint and endpoint metrics in life-cycle impact assessment
Midpoint and endpoint impact categories (or metrics, but not all impact categories can be converted into metrics) are the concepts in the area of life-cycle assessment studies.
Midpoint impacts are precursors to some endpoint impacts that we care about. For example, greenhouse gas emissions are a midpoint impact that leads to climate change and, ultimately, to human loss of life due to food shortage, flooding, wildfires, and other catastrophic events, as well as loss of animal life and entire animal and plant species (endpoint impacts). For another example, ozone depletion is midpoint impact and increased cancer rates (because less UV radiation from the sun is blocked) is an endpoint impact.
Some impacts could be considered both midpoint and endpoint, e. g. loss of ecosystems is both an endpoint impact in itself, but also decreases the quality of life, prosperity, or even leads to famine among people who lived off these ecosystems.
The impact categories of raw material production for batteries
There are three aspects of raw material assessment of batteries that can't be reduced to each other and therefore should not be integrated into a single metric: resource depletion, supply chain risk, and environmental and social impacts of mining.
Resource depletion
Olivetti et al. synthesized the available data on consumption rates relative to available reserves for nickel (Ni), manganese (Mn), cobalt (Co), lithium, (Li), and natural graphite. They found that the ratio of known reserves to primary mine production (also known as the static depletion index) has increased for Co, Li, and natural graphite, suggesting that continued demand has resulted in additional exploration and extraction. Mn and Ni did not show an upward or downward trend, indicating that the ratio of production to known reserves has remained relatively constant.
Interestingly, lithium iron phosphate (LFP) batteries are often praised to be better than batteries with Nickel-based cathodes because they only require "earth-abundant" materials. However, if we are to produce 2 TWh of LFP batteries per year by 2030, with 500 Wh/kg of cathode energy density of LFP, and Phosphorous being 19.6% of LFP cathode by mass, 784,000 metric tonnes of phosphorous will go yearly into batteries alone. This is comparable to 910,000 tonnes produced presently. Could this contribute to the problem of peak phosphorous? I didn't find any discussion of this whatsoever. Phosphorous is abundant in the rocks all over the Earth but is not economical to extract to produce fertilisers. Maybe this is not a problem for batteries, because they can easily withstand become several times more expensive without affecting the total cost of batteries much? Even if so, there could be a market-driven risk here: LFP manufacturers will use cheaper phosphates in the short term, making the future phosphate shortage problem for fertiliser production more acute.
Supply chain risk
Supply chain risk is a geopolitical risk associated with highly concentrated production, which can lead to conflict, price instability, and artificial shortages. Cobalt reserves and mining production are concentrated in DR Congo, but 95% of cobalt refining happens in China. China also produces 64% of the world's graphite and 55% of aluminium. Morocco has 70% of the world's phosphate reserves.
Environmental and social impacts of mining
In DR Congo, there have been serious environmental and social consequences of copper and cobalt mining, ranging from child labour to human exposure to heavy metals, particularly from unregulated artisanal and small-scale mining operations.
Cell manufacturing is about two times more energy-intensive than mining and production of the raw materials for the cells
In other words, cell manufacturing accounts for two-thirds of energy consumption in cradle-to-gate LCA assessment for cells (source).
Evaporating the NMP solvent (after coating cathode slurry on the current collector foil) and maintaining the facility's dry room conditioning together consume about 80% of energy spent during cell manufacturing. However, the energy usage estimates for dry room conditioning were obtained on small-scale facilities and can drop by an order of magnitude on a very high-throughput cell production line.
Nickel-Manganese-Cobalt (NMC) cathode production can be two to three times more energy-intensive than the production of other cathode materials (LMO and LFP), and therefore also become a major contributor to the total energy spent during cell manufacturing.
Northvolt Ett's cell manufacturing energy use is 50 kWh per kWh of cell capacity produced.
Energy stored on energy invested (ESOI)
Energy stored on energy invested is a metric that has been proposed by Barnhart and Benson for "cradle-to-gate and use" and "cradle-to-grave" life cycle assessments of energy storage technologies:
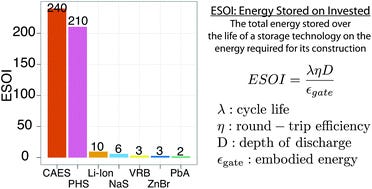
For recyclable batteries, I think that a metric like cradle-to-grave energy efficiency would be more convenient because it could be directly used in downstream calculations such as assessing energy efficiency or EROI (energy return on investment) of renewable or nuclear power installations with accompanying energy storage for daily power balancing and manoeuvring, as well as in lifecycle greenhouse gas emission comparisons between internal combustion, hybrid, and fully electric vehicles for different carbon intensities of the grids in different countries.
There are several factors that make it difficult to estimate battery's ESOI or cradle-to-grave efficiency:
The fact that different batteries are used differently (e. g., charged and discharged slower or faster, different number of hours per day, with different shelf life before they begin operation, at different ambient temperatures, etc.) directly affect the expected lifetime and the round-trip efficiency of the battery.
Most batteries originally manufactured for electric vehicles are expected to enter a second-life phase in energy storage with a very different usage pattern, but the exact moment when it happens is uncertain.
Battery's capacity and internal resistance change during its lifetime. The internal resistance affects the round-trip efficiency directly, and the capacity can affect the usage pattern.
As of 2021, there are many things to improve in lifecycle assessments of batteries, both in literature and industry
LCAs should start using country-specific raw material production impacts rather than the industry averages (or, even worse, the current industry's state-of-the-art or best-practice impacts). They should also consider the differences between average, marginal, and incremental sources of key material inputs, in conjunction with projections of the global demands for these materials, as the global Li-ion battery production quickly rumps up. We should also create and use methods for capturing the effect of outliers and "superemitters"/"superimpactors" in mining and material processing.
The assessments should correctly present the uncertainty. A single-number metric value conveys false precision. (Steve McConnell advises for exactly the same in his book about software estimations.)
We strongly recommend that future LCAs make an attempt to separate impacts tied to energy use with those tied to other activities. If facilities shifting their fuel use to lower-emission alternatives (e.g., from coal to natural gas, or natural gas to renewable fuels), making this distinction in published LCAs will make it easier to adjust the results accordingly.
Water consumption and withdrawals associated with battery production can be substantial, yet it is often overlooked in LCAs. Battery electric vehicles are associated with over 50% more water use relative to internal combustion engine vehicles over the course of their lifetime. This is mostly associated with the electricity use associated with vehicle charging, but a large contribution of water consumption is attributable to the LIB itself, consisting of 5–10% of the total water consumption depending on the battery chemistry.
As long as underlying assumptions about cycle life are clearly documented, the authors suggest that life cycle assessments would be well served to report results normalised both per kWh of battery capacity and per kWh of lifetime throughput.
On including a few most important impact metrics in lifecycle assessments vs. categorising all metrics
If a particular assessment doesn't cover some impact (aspect, dimension), it should still mention this explicitly. Omitting an impact category may lead readers to believe it is not important.
On the other hand, comprehensiveness comes at a cost. Selecting life-cycle inventory, midpoint, and/or endpoint metrics that are likely to yield the greatest insights (and have sufficiently high-quality data to support those conclusions) will make LCAs more interpretable and impactful.
Counterfactual life-cycle assessment of batteries and electric vehicles vs. internal combustion engine vehicles and fossil fuel power generation
Exhaustive, overly-pedantic categorisation of all the impacts of battery production and use can also confuse the public towards thinking that batteries are actually very "dirty" in production and recycling compared to the lifetime of fossil fuel combustion in ICE cars. Fossil fuel advocates could also refer to these comprehensive battery assessments to spread FUD instead of comparing them counterfactually with the effects of keeping internal combustion vehicles and gas power generation running.
So, I think it's valuable to include counterfactual comparisons with fossil fuel alternatives in battery and other clean energy LCAs as a protection against such abuse.